Le Tamahagane

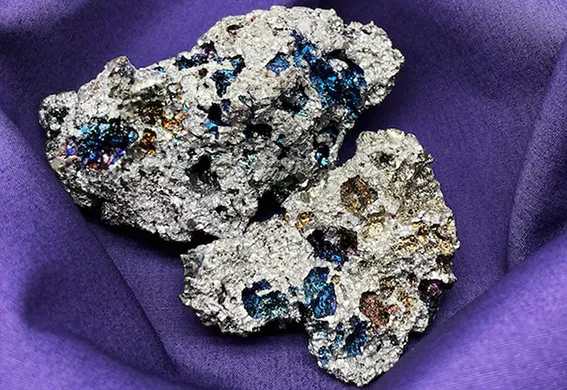
Le fer miraculeux des sabres japonais
La production de sabres au Japon débute avec la création du "Tamahagane", il s’agit là d’une entreprise artisanale exceptionnelle.
Reconnu pour sa combinaison de solidité et de flexibilité, le Tamahagane résiste également à la rouille, ce qui en fait un fer véritablement remarquable, difficile à forger même avec les technologies les plus avancées.
Matériau d'exception, le Tamahagane demeure inégalé pour la fabrication des sabres japonais, ils sont universellement salués comme les œuvres d'art en fer les plus raffinées de l'humanité.
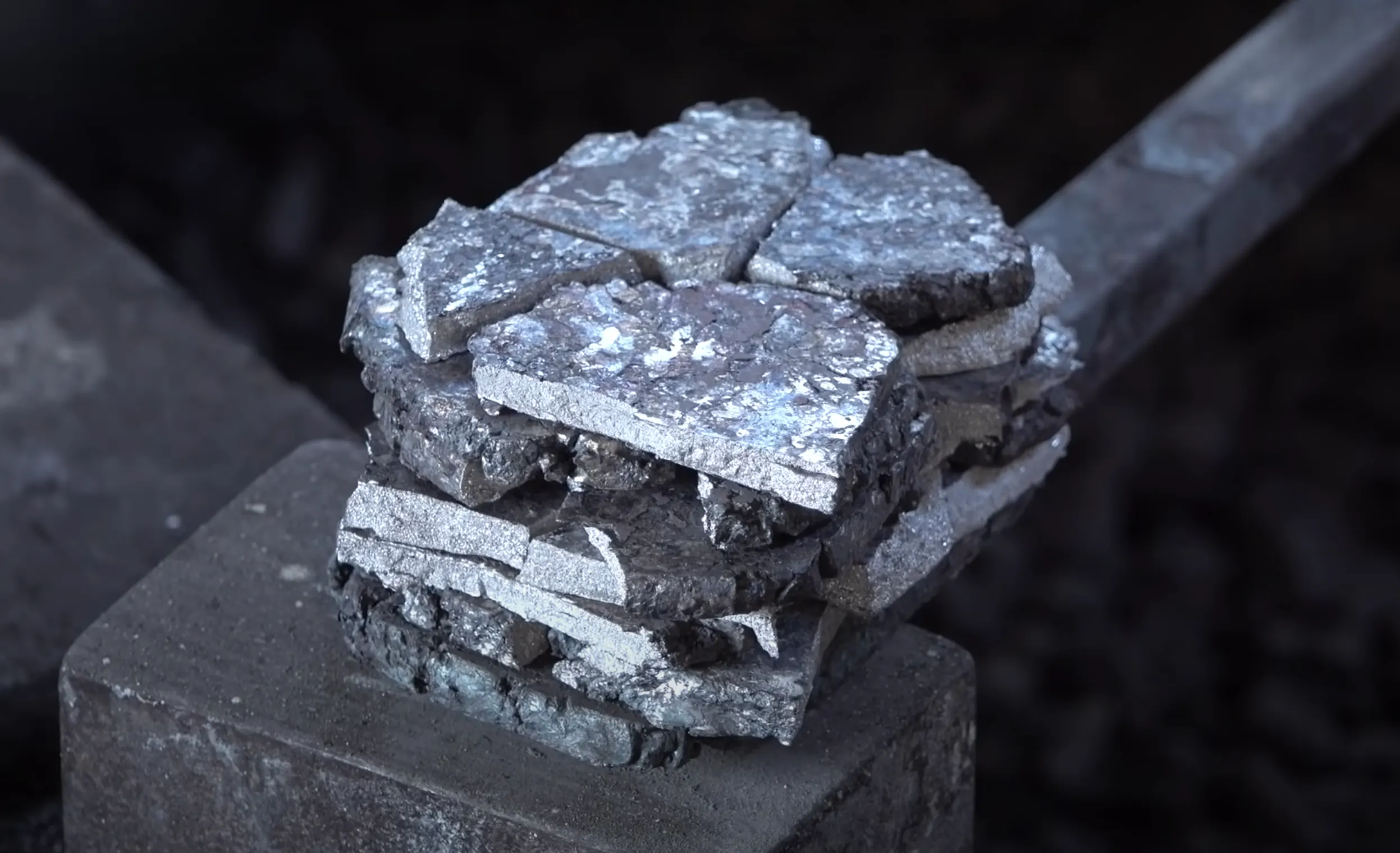
Avec la technique de bas fourneau japonaise "tatara", la répartition du carbone dans le fer n'est pas uniforme et peut être considérée comme un inconvénient lorsqu'on vise à obtenir de l'acier présentant des propriétés mécaniques de haute qualité.
Cela est particulièrement crucial dans des applications telles que la fabrication d'un sabre traditionnel japonais. Dans ce processus, le forgeron sélectionne méticuleusement les morceaux les plus précieux de la loupe (kera), les assemble à la forge pour former un lingot, puis procède à une série d'étirements et de pliages successifs du lingot, une technique connue sous le nom de "feuilletage".
L'objectif de cette méthode est d'homogénéiser les différentes couches de fer présentes dans le lingot, en fusionnant celles qui contiennent une quantité excessive de carbone avec celles qui en renferment peu ou pas du tout. Ce processus complexe permet ainsi de créer un acier composite d'une qualité exceptionnelle, où les caractéristiques souhaitées telles que la résistance et la flexibilité sont soigneusement équilibrées.
La fabrication du Tahamagane
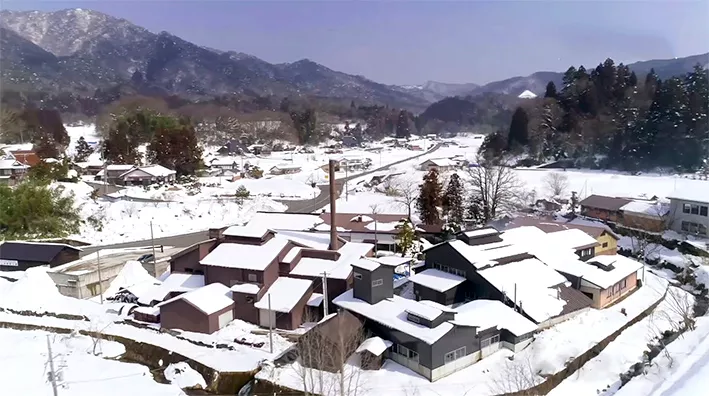
La ville d'Okuizumo dans la préfecture de Shimane est la seule forge au monde qui fabrique du tamahagane pour les sabres japonais.
Il fut un temps, il y a plus de cent ans, où la région d'Okuizumo était le principal centre industriel du Japon. Les rizières en terrasses étaient exploitées pour l'extraction du sable de fer, alimentant ainsi une industrie florissante du fer tatara. Même aujourd'hui, si l'on dirige un aimant vers la rivière Hiikawa qui traverse Okuizumo, on peut aisément détecter la présence de sable ferreux.
Dans la région montagneuse du versant Sanin des montagnes Chugoku, connue pour son sable de fer de haute qualité, les montagnes ont subi une dégradation importante. Le sol a été érodé par l'eau, et le sable de fer a été recueilli dans des étangs peu profonds organisés en étagères. La fabrication du fer Tatara dans cette région utilisait le sable de fer comme matière première. Jusqu'au début de l'ère Meiji, avant l'introduction de la sidérurgie moderne de style occidental, cette région était responsable de plus de 80 % de la production de fer au Japon.
Le Tatara
"Tataraba", Le processus de fabrication du tamahagane dure quatre jours et il commence toujours par un rituel shinto pour prier pour son succès.Le processus de fabrication du tamahagane est d’une simplicité trompeuse. Les matériaux, sable de fer et charbon de bois, sont versés dans le four en argile où le charbon de bois brûle par le haut toutes les 30 minutes pendant trois jours et trois nuits. Le sable de fer chauffé au charbon de bois augmente sa pureté à mesure qu'il tombe au fond du creuset et se solidifie. Le morceau de fer ainsi créé est appelé "Kera".
Un tamahagane argenté se forme à l'intérieur du four, mais le rendement ne peut être déterminé que lorsque le four est brisé et que l'intérieur est examiné.
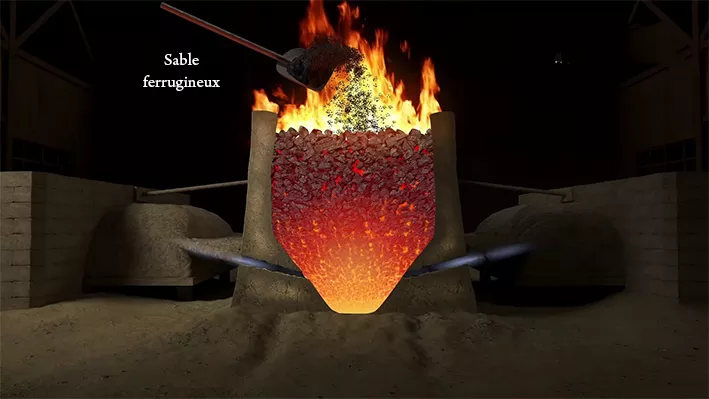
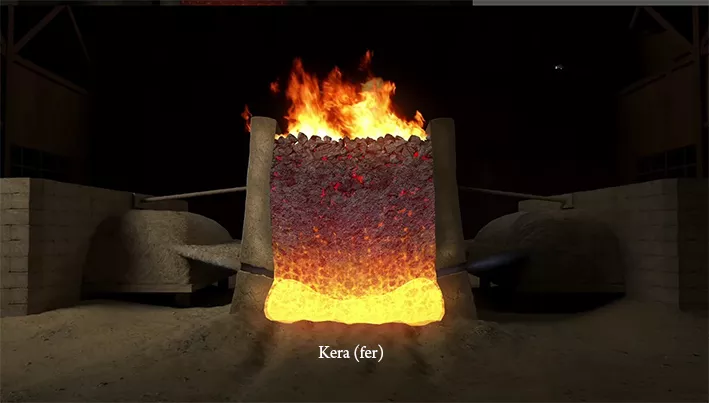
La fabrication du tatara débute par la préparation du sol.
C'est un travail qui dure environ trois jours pour créer le sol qui servirait de base à la fabrication du four.
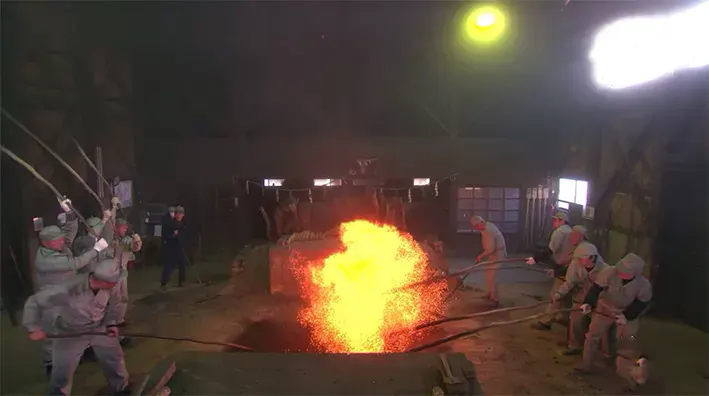
Une fois le sol préparé, la contruction du four peut commencer.
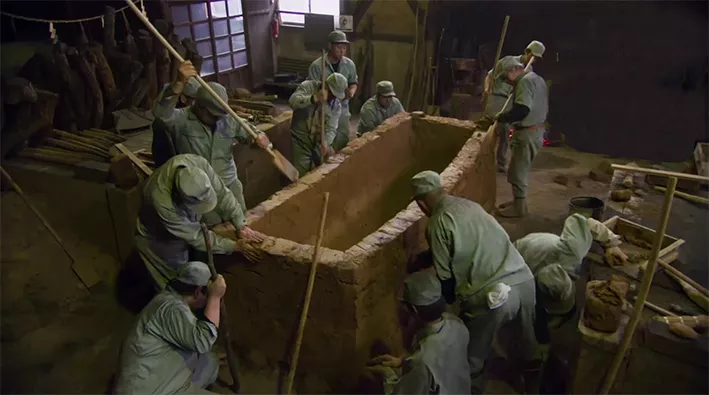
Commence alors le chargement du four avec le charbon de bois puis une fois celui-ci allumé, le versement su sable ferrugineux.
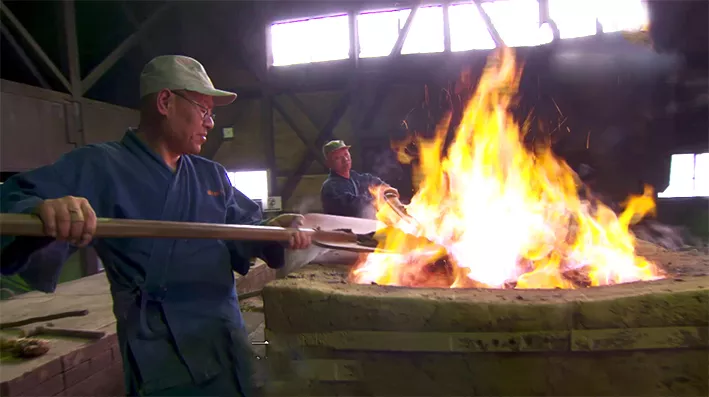
Deux trous à la base du four permettent l'évacuation des scories durant le processus.

Durant 3 jours les artisans vont se relayer pour surveiller et alimenter le four.

Au bout de 3 jours de travail intensif dans une chaleur infernale, le travail est terminé et le tatara va être cassé pour libérer le Kera, la boule de fer contenant le tamahagane.
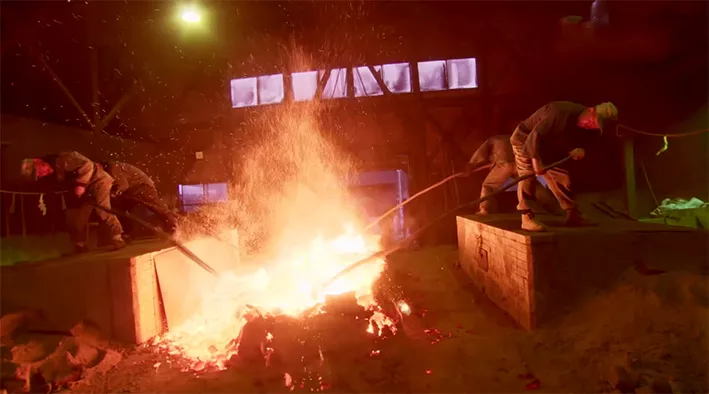
Le résultat de ces 3 jours de travail, une boule d'acier d'environ 3 tonnes.
Elle a été obtenue par la fusion de 8 tonnes de sable et 13 tonnes de charbon de bois.
Ce métal, caractérisé par une faible teneur en soufre (attribuable à l'utilisation de charbon de bois) et en phosphore (absent dans le minerai), est néanmoins significativement contaminé par divers résidus métalliques. Il incombe au forgeron de maîtriser l'art de les éliminer. De cette masse d'acier, la majeure partie est destinée à la fabrication d'articles courants. Environ 500 kg possèdent les propriétés requises pour la production d'armes, dont 180 kg sont constitués d'un acier à la composition spécifique (à haute teneur en carbone) : le Tamahagane.
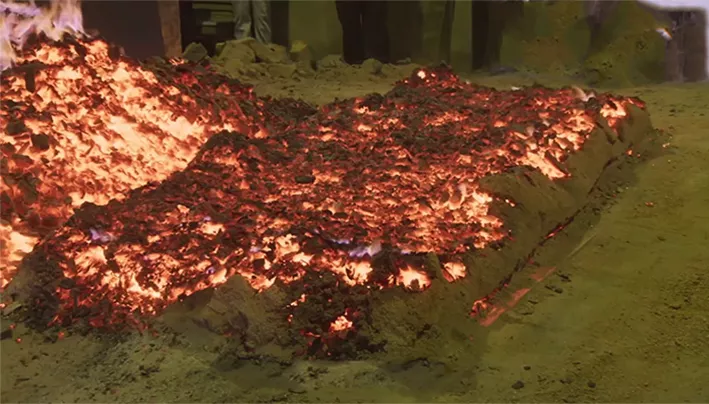
Les sabres japonais forgés
à partir de l'acier Tahamagane sont ce qui se fait de mieux en terme
de qualité et beauté de l'acier.
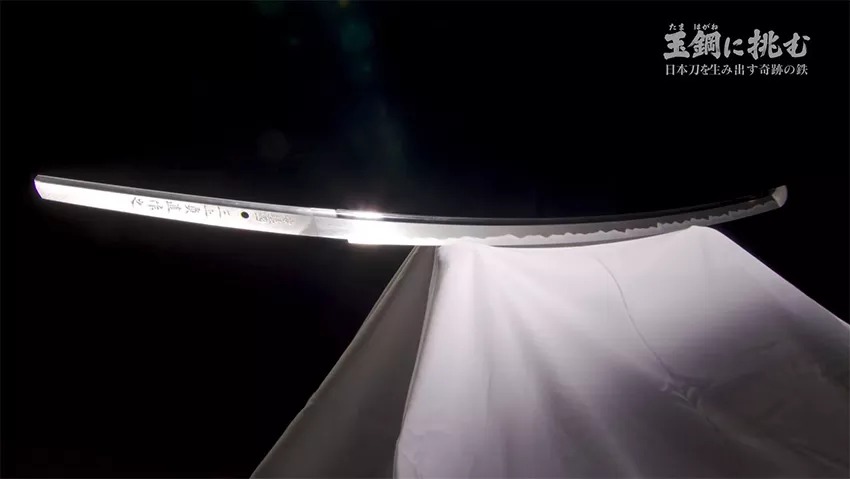